美国空军网站4月4日消息,空军主要研发中心空军研究实验室的制造与工业技术部正与承包团队合作,开展一项研究工作,量化用新发动机进气道工艺替换旧制造工艺的优势。
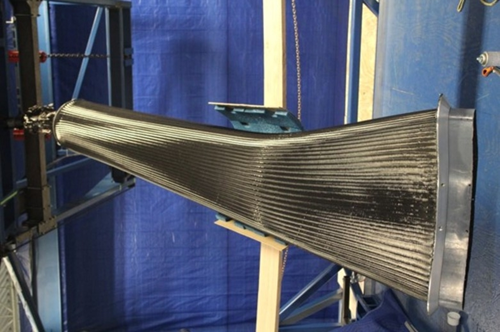
飞机发动机进气道能持续为发动机压缩机提供空气,防止压缩机失速。由于进气口直接暴露在冲击气流中,因此必须将阻力最小化。一旦气流供应中断,哪怕极短的时间,也会导致发动机出现严重问题,造成严重的效能损失。
如果进气道要保持用最小的湍流提供充足的空气,就必须保持清洁和没有缺陷。进气道的传统制造过程是:用合成树脂预浸合成材料,手工涂抹到多件式心轴上。心轴进行包裹后会放入高压釜中进行加工。高压釜是一种热加压容器,能提供热量固化树脂,提供压力确保完全固化后的复合材料部分吸水性降至最低。
替代工艺是,用自动涂覆替代手工涂抹过程,且在心轴上涂覆的不是预浸复合材料,而是干纤维。原来沉重的钢制多件式心轴换成了轻质单件式聚合材料心轴。干燥的纺织碳纤维用低成本的环氧树脂,采用真空辅助树脂传递模塑工艺进行了处理。
由于进气管的形状比较复杂,制造程序要经过多次迭代才能优化纺织机的设定,从而最大程度减少复合材料起皱。研究组将总共制造四个进气道,以比较新设计进气道与旧进气道在成本和生产时间方面的优势。
进气道成品会提交给政府,以便进一步整合到机身设计和制造程序中。